
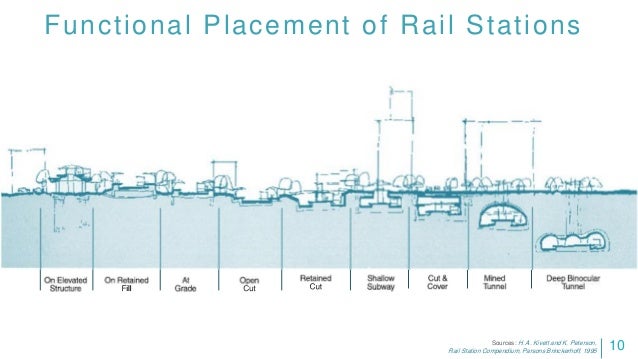
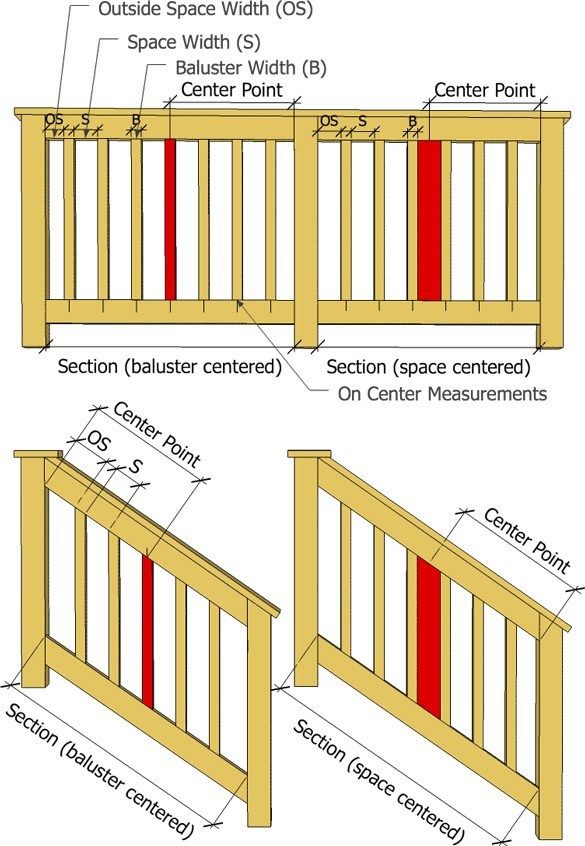
When calculating the vertical offset, the height tolerance, H, of the carriages must be taken into account. If this value is exceeded, a roll moment will be introduced into the carriages, which can result in shortened bearing life. This is often specified as S1, and is a function of the distance between the rails and the preload of the carriages-the higher the preload level of the carriages, the smaller the permissible vertical offset. Rails used in parallel should also adhere to the maximum permissible offset in the vertical direction. Vertical offset between rails Vertical offset between rails, S1 This is because when there is no lateral retention, the shear strength of the rail mounting screws becomes the limiting factor for permissible side load. It’s important to note that if the rails are not mounted against a reference edge or retaining strip, the permissible side forces may be reduced. There are many options for securing the rails and ensuring their straightness, ranging from the most precise method of using a machined reference edge for each rail, to the least precise (and least costly) method of mounting one rail using a straight edge or gauge, and using a connecting plate to “float” the second rail into proper alignment. But regardless of the number of carriages, when two rails are used in parallel, extra side loads can result if they are not mounted within the manufacturer’s specified parallelism tolerance, often denoted as P1. The most common installation of linear rail guides is a two-rail, four-carriage arrangement. Rail parallelism Parallelism between rails, P1 Understanding and following the three mounting specifications described below will help ensure your installation achieves the desired accuracy and doesn’t succumb to premature failure. But improper mounting can add unnecessary loads, reduce life, and undermine the inherent travel accuracy of the linear guide system.
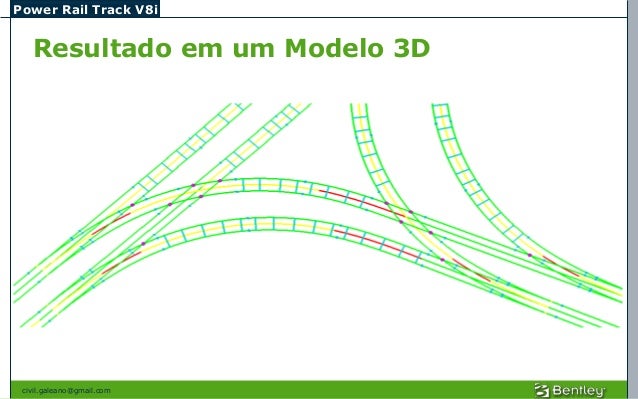
Linear rail guides are designed for applications that call for precise motion with high load-bearing capability.
